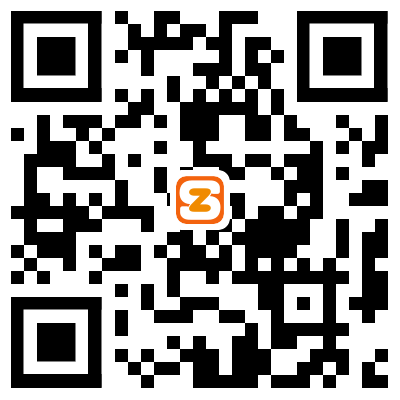
去料頭技術-模內熱切廠家-模內熱切視頻
價格
訂貨量(個)
¥4000.00
≥1
店鋪主推品 熱銷潛力款
㠗㠚㠖㠒㠖㠓㠖㠖㠒㠔㠓
在線客服
在注塑成型之后,水口連接,多數為人工修剪,勞動強度大,而修整難以使其美麗漂亮。目前,塑料部件的使用急劇增加了塑料的質量。但是,由于原材料價格上漲,工人工資,加上市場競爭日益激烈,企業的利潤下降,如何降低成本?通過技術改進,它還提高了產品的質量,實現自動化生產是塑料生產企業的緊迫任務。
邦注科技模內切工作原理
什么是模內熱切技術?
模內熱切技術就是產品在模具里未被頂出狀態的時候實現產品與水口的熱分離技術;
模內熱切系統包含單元:超高壓時序控制系統、微型超高壓油缸、高速高壓切刀。
切刀與產品硬切嗎?
切刀與產品是軟切,真正意義上是擠壓, 將多余的料擠到溢料槽內;
模內切水口技術背景
注塑成型后,澆口鄰接,人為澆口處修剪,勞動強度大,修剪很難平整好看。目前關于塑料件的使用量之大,使塑料的生產量與品質快速上升;但由于近年、人員工資、原材料價格等成本的上漲,加上市場競爭日趨激烈,企業的利潤在不斷下降,如何降低成本?又能提高產品表面質量,通過技術創新、 完成自動化。
生產是大多塑料生產企業迫在眉睫的大事。
現有的辦理方法是開模前從頂板上頂出切刀將澆口分離,是在開模后開始剪切,由于此時料已經冷卻,剪切后的澆口面不平整好看,產品品質上不去,依舊需要多次手動修剪才可將切口弄平整,勞動強度仍舊較大,擴充了人工成本。此外,現有技術模具內無法實行自動化剪切,其原因主要兩點:一是以往的油缸體積過大,模具內的空間無法滿足體積大的油缸安置;二是油壓設備的壓力無法達到自動化剪切的力度。
模內切產品的價值
為了克服上述現有方式的不足,本公司發明了一種模具內自動剪切裝置,切除產品和料頭的鏈接部位,確保澆口切面的平整性,同時也降低勞動強度
本公司自主研發的產品:模具打開后產品和澆口已經分開,無需人工剪切可以直接包裝出貨,提高生產速度及節省人工成本
模內熱切成型的自動化,避免了生產過程中無用的人為動作,而產品的全自動化機械剪切保證品質一致性 ,在產品大規模生產過程中較傳統的模具有著不可擬比優勢。
邦注科技模內切工作原理
什么是模內熱切技術?
模內熱切技術就是產品在模具里未被頂出狀態的時候實現產品與水口的熱分離技術;
模內熱切系統包含單元:超高壓時序控制系統、微型超高壓油缸、高速高壓切刀。
切刀與產品硬切嗎?
切刀與產品是軟切,真正意義上是擠壓, 將多余的料擠到溢料槽內;
切刀在什么時候頂出?
理論上切刀在保壓完成時頂出;
模內熱切具體動作介紹:
注塑分為三部分:射膠(軟料)+保壓(軟料)+冷卻(硬料) 當產品保壓完成后切刀頂出,將產品與水口進行分離,切刀保持頂出狀態,等 到產品冷卻完成前2S,切刀退出,模具打開后,產品與水口呈分離狀態。
什么是模內熱切技術?
模內熱切技術就是在產品沒有頂出的時候實現產品與水口的熱分離技術。
切刀在什么時候頂出?
切刀在保壓完成時頂出。
切刀與產品硬切嗎?
切刀與產品是軟切,真正意義上是擠壓,將多余的料擠到溢料槽內。
模內熱切具體動作介紹:
注塑分為三部分:射膠(軟料)+保壓(軟料)+冷卻(硬料)
當產品保壓完成后(料還未完全冷卻)切刀頂出,將產品與水口進行分離,切刀保持頂出狀態,直等到產品冷卻完成前2S,切刀退出,模具打開后,產品與水口呈分離狀態。
模內熱切系統包含單元:
超高壓時間控制系統+油管(連接時間控制器與模具)+微型油缸+切刀+觸點開關
一、為什么要選用模內熱切?
現在制造業面臨問題:
1.供需不協調、訂單波動與資源難以取得平衡;
2.社會成本高漲,人力成本越來越高;
3.資源缺乏,勞動意識提升,效能降低;
二、使用模內熱切之后:
1.模內自動化,降低對人的依賴度;
2.降低成型周期;
3.生產穩定性提高;
4.降低產品人為品質影響;
5.降低模具維修成本。
三、無錫邦注科技有限公司模內熱切整體優勢與服務保障
1):公司提供完整的熱切相關模具零配件,模具上只需要預留裝配特征,不需要客戶端自備加工零件。
2):所有產品包括控制器,切刀,油缸,相關鏈接配件均標準化,模塊化。
3):為客戶提供標準化電子檔,方便客戶端設計使用。(有標準的電子資料庫為客戶提供簡單快捷的操作環境)
4):提供客戶包括設計,加工,鉗工,試模調試等,全面標準化教材。(全面化教材涵蓋切刀設計規范,模具油路設計規范,切刀導向塊設計規范,澆口設計方案履歷,產品應用實例等)
5):提供客戶對模內時序控制,全面教育訓練課程。